Servo Settings for BLS5400 Series Xact Servos
- AIRBOSS RC
- Dec 18, 2023
- 2 min read
Updated: Dec 21, 2023
Setting up your servos requires precision and accuracy. Xact servos require specific settings to ensure they run properly. Here are the settings we recommend you use to run BLS5400 Series Xact Servos:
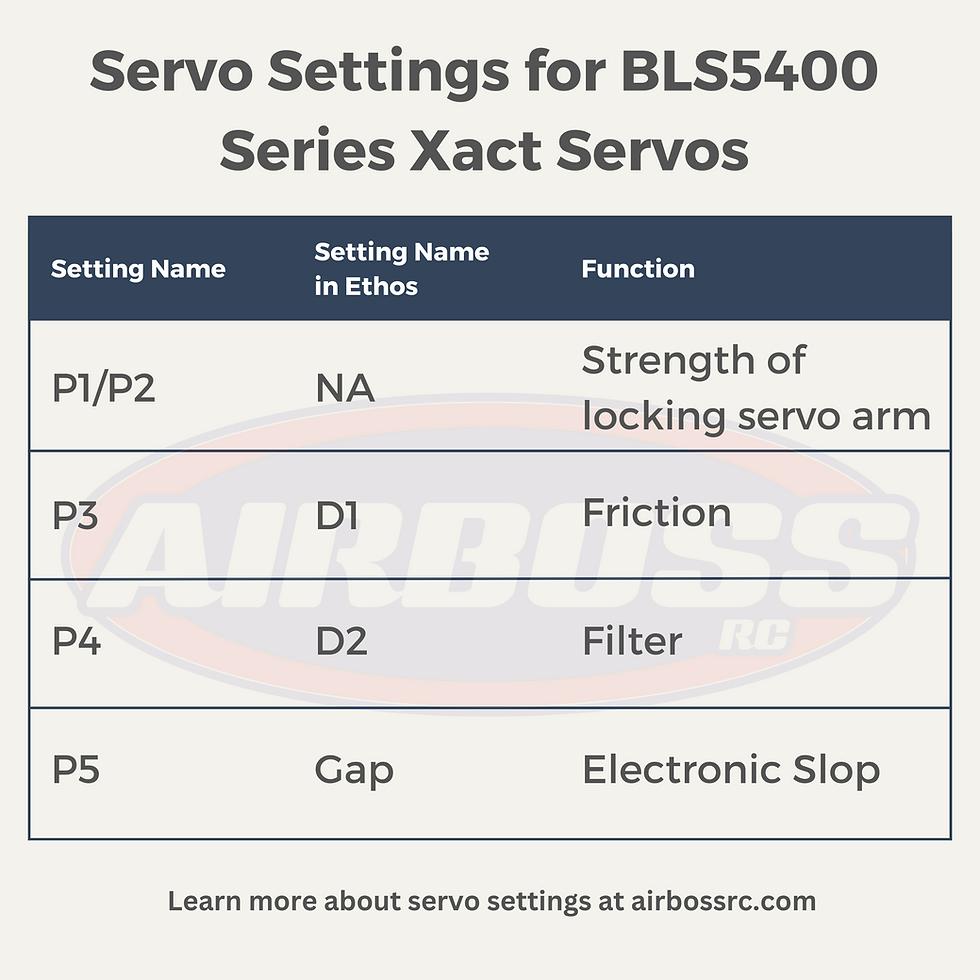
These settings should be adjusted for each individual's project based on testing.
Data Rate
Data rate is the frequency at which the the telemetry is communicated back and forth between servos, receivers, and transmitter. The number of data rate indicates how quickly the telemetry data is being communicated across your system.
The higher the data rate number, the less frequent the communication will be. The lower, the faster the refresh and more frequent the communication.
During testing, we found an issue when trying to run a faster refresh rate. Anything under 25ms created a problem.
We recommend 100ms, which is one-tenth of a second refresh. We find that this provides an ample amount of telemetry.
P1
P1 decides the force strength of the locking servo arm. The bigger the P1 is, the bigger the strength given to the lock arm.
If P1 is set too small, then the servo arm can be moved easily.
P1 to P2 Ratio
The ratio of P1/P2 affects the speed and jitter performance of the servo: the bigger the ratio is, the faster speed the servo moves.
The downside of this is that faster speed lowers precision. Due to this reason, in this case, the servo arm would always look for the final stop point around the endpoints. It appears to show the "jitter" pheneomenon while stopping/landing on the ground.
Otherwise, the smaller ratio of P1 to P2 creates higher precision, so there should be no jitter while landing.
P3
P3 is a compensative value to the P1. As formentioned, if P1 is too big, then the ratio of P1/P2 is bigger, and "jitter" will happen while stopping/landing.
So make the P3 a bit bigger to compensate the P3 in this case, and the "jitter" phenomenon should be improved. But it does not mean the bigger P3 is, the better performance it would give.
Bigger P3 compensates almost every moment while the servo is moving, so it would bring jitter or moving with a stutter.
P4
P4 is a filter parameter. It ranges from 0 to 15. It will default to 7 and it is not necessary to change.
P5
P5 represents electronic deviation. This value is used for matching the mechanical deviation. For example, the pure mechanical deviation is 0.3 degrees, then the P5 is normally set to 2, not exceeding 3 at the most.
P5 cannot be set larger than the actual mechanical deviation. The deviation would become big otherwise, and would not be sufficient to lock the servo arm.

If you need help or have questions about your servo settings, reach out to us sales@airbossrc.com or 903-497-6718.
Comentarios